Qualità
Certificazione
ISO 9001
Per Verbrugge la vostra soddisfazione è la priorità
Qualità certificata
Per garantire la massima qualità ai nostri clienti, abbiamo recentemente rinnovato con successo la certificazione ISO9001, che definisce i requisiti del sistema di gestione della qualità per la produzione industriale.
Scegliendo Verbrugge, beneficiate di una tracciabilità completa e di una perfetta riproducibilità di tutti gli ordini.
Abbiamo la capacità di soddisfare le richieste più specifiche e i nostri principali clienti confermano la loro soddisfazione per i servizi Verbrugge: scegli le nostre soluzioni!
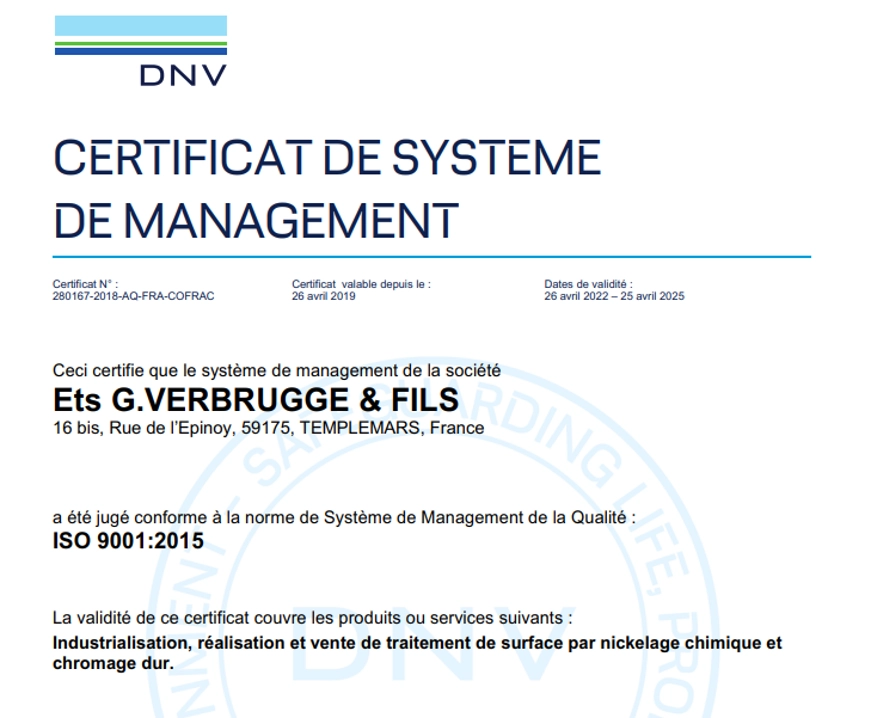
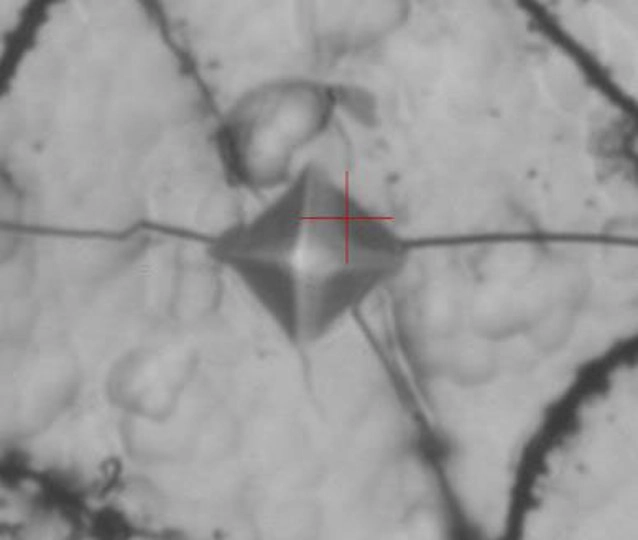
PROVE DI DUREZZA CON MICRODUROMETRO VICKERS LEITZ
La durezza è la misura della resistenza di un materiale alla penetrazione di una forza costante e regolare. Generalmente identificato con un tester di durezza penetrante, viene utilizzato per misurare le dimensioni delle diagonali dell’indentazione in seguito al rilascio di un carico, al fine di determinare la durezza.
Il materiale più duro è il diamante, talmente duro da essere utilizzato principalmente come materiale da penetrazione (per la durezza Vickers in Hv).
Esistono relazioni più o meno dirette tra durezza, resistenza meccanica e tenacità. In generale, più un materiale è duro, maggiore è la sua resistenza meccanica, ma più è fragile.
Un esempio tipico è la ghisa, che si differenzia dall’acciaio per avere un contenuto critico di carbonio che fa precipitare i carburi, rendendo il materiale molto resistente e tuttavia molto fragile.
In conclusione, il termine “solidità” di un pezzo non può essere legato solo alla sua durezza. La solidità è definita in base all’uso che se ne fa. La scelta di un materiale “solido” è quindi sempre un compromesso tra durezza, resistenza meccanica e tenacità, a cui va aggiunta la resistenza alla corrosione, alla fatica o allo scorrimento, a seconda dell’uso previsto.
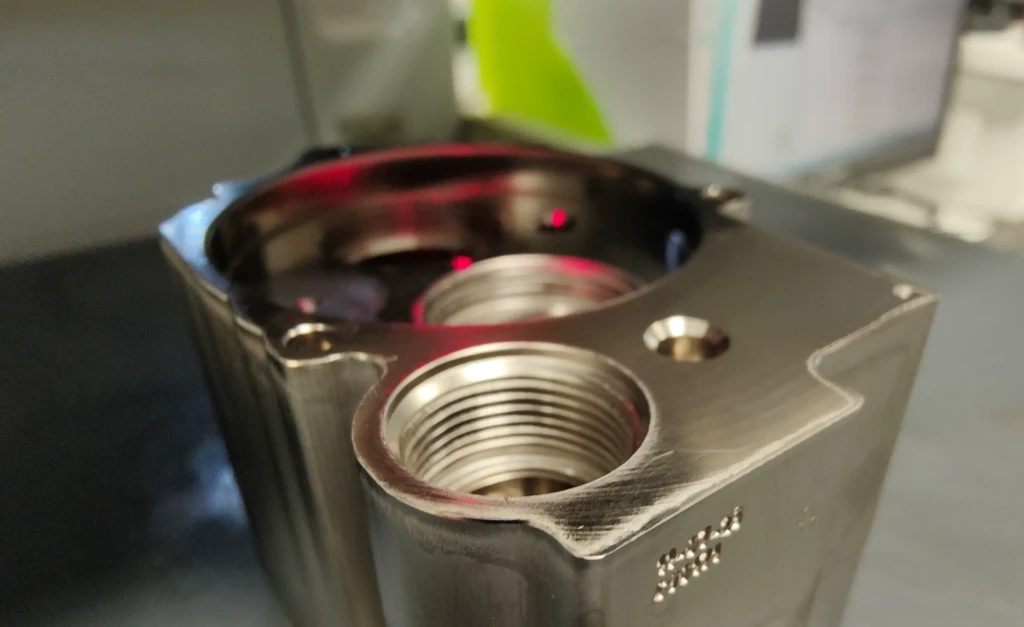
CONTROLLO DELLO SPESSORE MEDIANTE FLUORESCENZA A RAGGI X
Quando un materiale è sottoposto a fluorescenza, emette energia sotto forma di raggi X: si tratta della fluorescenza a raggi X o dell’emissione secondaria di raggi X.
Lo spettro dei raggi emessi dal materiale è caratteristico della composizione del campione. Questo ci permette di dedurre la sua composizione elementare, cioè le concentrazioni di massa degli elementi, per determinare il suo spessore al micron più vicino.
Le nostre conoscenze ci permettono di effettuare controlli di spessore sul nichel utilizzando la fluorescenza a raggi X.
Caratteristiche:
– Controllo spessore dei rivestimenti da 2μm a 30μm.
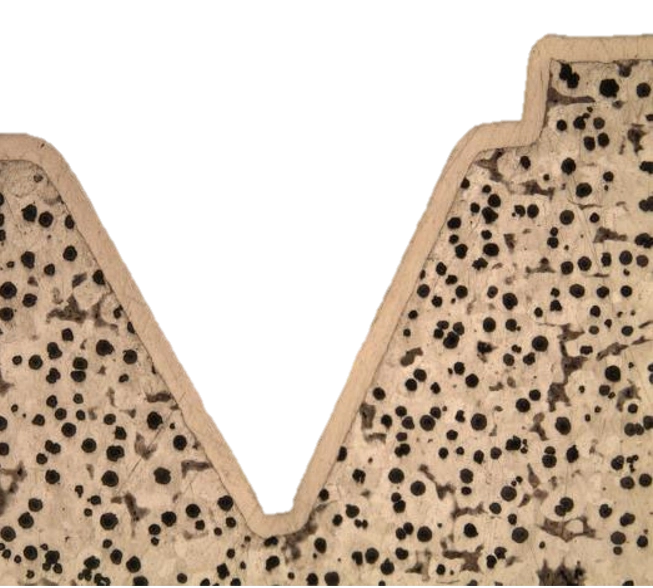
SEZIONE MICROGRAFICA
Sui campioni di prova viene eseguita una sezione micrografica. Inseriti nel bagno, seguono i pezzi attraverso i vari trattamenti e ricevono lo stesso rivestimento.
Si tratta di un test distruttivo effettuato su un campione, utilizzando un microscopio ottico ed elettronico con un ingrandimento adeguato. Il rivestimento è evidenziato da una sezione trasversale del pezzo.
In Verbrugge siamo in grado di effettuare controlli di sezione micrografica sui nostri depositi.
Questo tipo di controllo è particolarmente ricco di informazioni. Viene utilizzato per misurare lo spessore di uno o più strati (che può variare da una a diverse decine di micrometri) per ottenere le informazioni necessarie su:
– la loro omogeneità, lo stato microstrutturale, la presenza di fessure, porosità e discontinuità;
– il profilo di rugosità del pezzo e del suo deposito;
– la qualità della sovrapposizione, in particolare intorno ai bordi e agli angoli vivi;
– modalità di guasto (visualizzazione delle fasce di degrado, stima della profondità di attacco);
– la salute metallurgica del materiale di base.
Caratteristiche:
– Controllo strutturale dei rivestimenti da 2μm a 500μm.
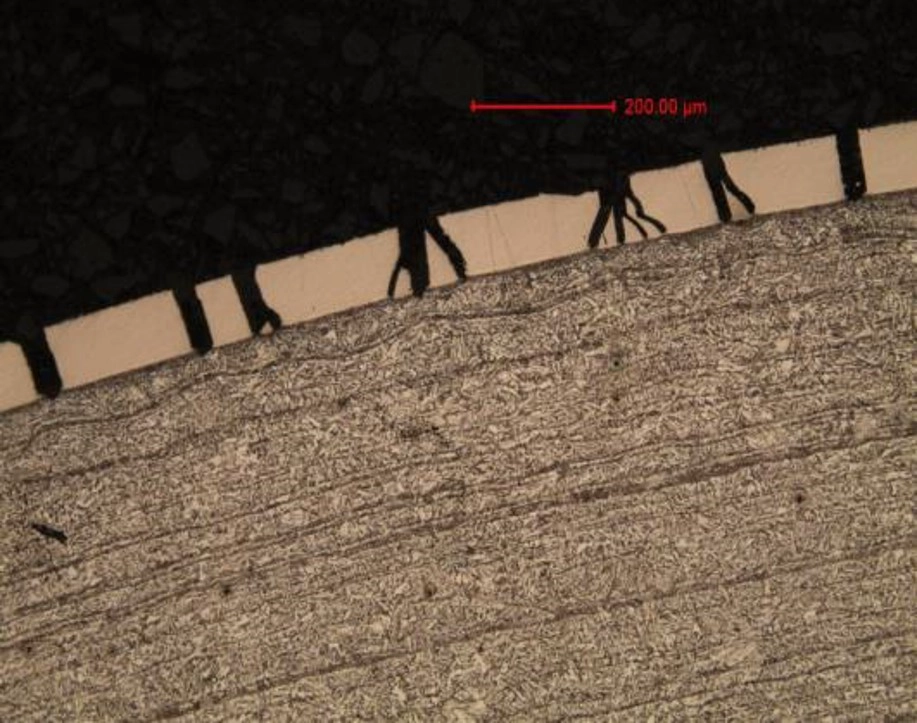
CONTROLLO DELL’ADERENZA
L’adesione è un parametro critico per molte applicazioni. Questo criterio ha un forte impatto sul comportamento meccanico e tribologico del rivestimento, nonché sulla sua resistenza a lungo termine alla corrosione.
A seconda del tipo di superficie e del suo utilizzo, i test di adesione saranno più o meno severi. In generale, la nozione di adesione di un rivestimento non è una proprietà intrinseca. I mezzi di controllo rimangono essenzialmente qualitativi e adattati alle condizioni di utilizzo dei rivestimenti e dei trattamenti superficiali.
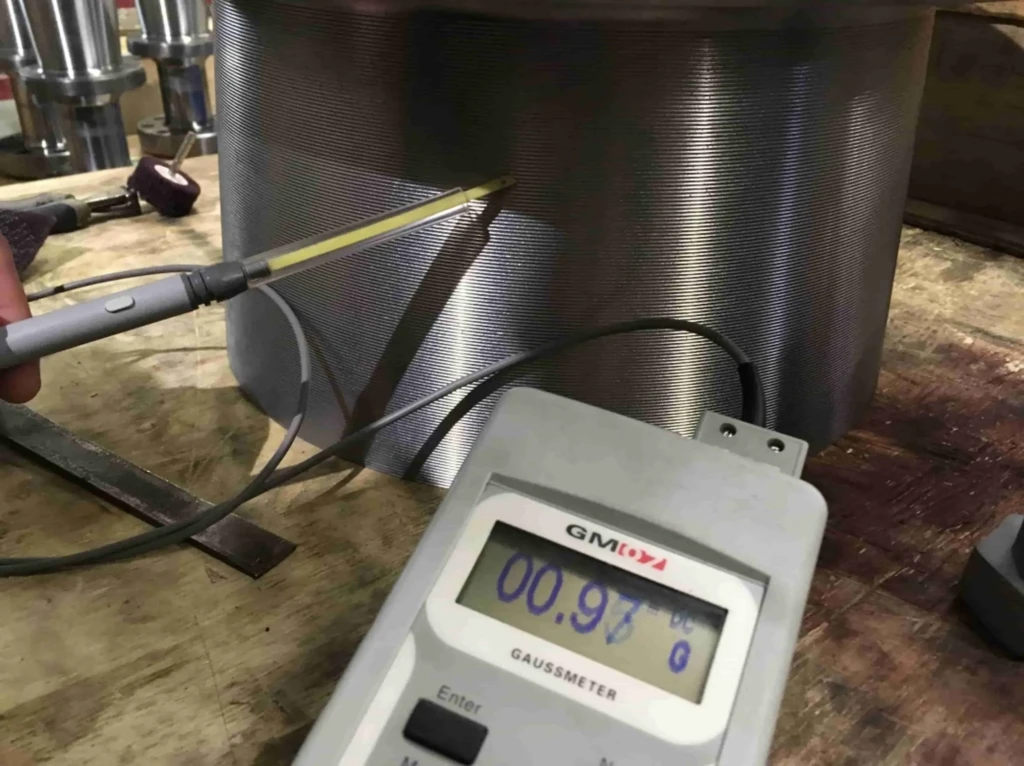
CONTROLLO DEL MAGNETISMO
Come suggerisce il nome, il controllo del magnetismo rileva il magnetismo rimanente dei componenti. Le misure vengono prese prima del trattamento con un gaussmetro che viene spostato su tutta la parte da trattare.
I pezzi con una forza magnetica residua anche bassa non avranno un rivestimento superficiale di qualità ottimale. Questo perché il deposito tenderà a non aderire correttamente e a raccogliere tutte le impurità presenti nei bagni.
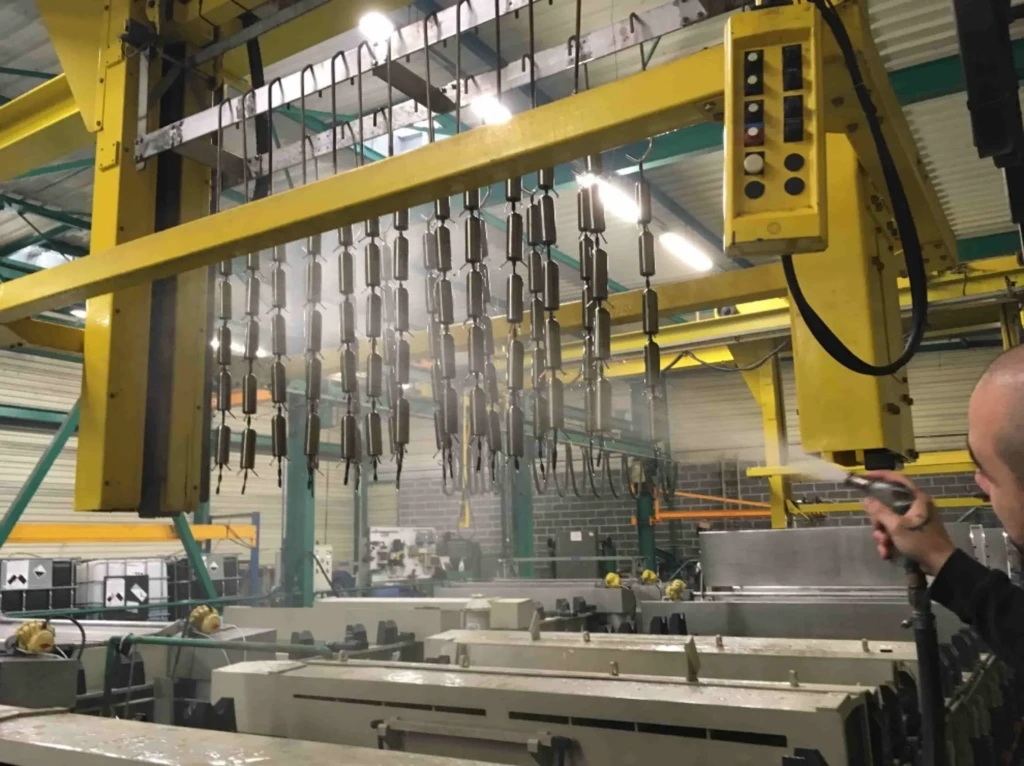
TEST DI BAGNABILITÀ
Il test di bagnabilità è visivo. Nel nostro caso, viene utilizzato per verificare la pulizia di un pezzo prima di procedere al suo trattamento.
All’arrivo presso la nostra sede (o dopo lo sgrassaggio), effettuiamo un test di bagnabilità osservando il comportamento di una goccia di un liquido calibrato posta sulla superficie del pezzo: più si diffonde, più il pezzo è grasso.
Questo test viene effettuato partendo dal presupposto che i nostri clienti utilizzano grassi difficili da eliminare prima del nostro trattamento.