Partager
Partager
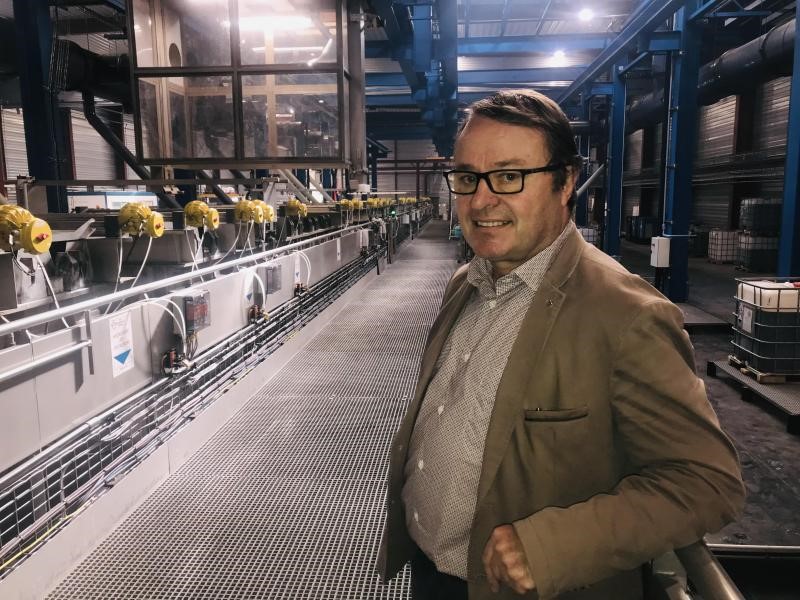
Finalement, le déménagement de l’entreprise familiale de chromage et nickelage Verbrugge de Lille à Templemars, soumise à autorisation de la préfecture, s’est déroulée sans accroc à la rentrée. Cette activité de niche va pouvoir se développer pour devenir leader européen.
Anne-Gaëlle Dubois | Publié le10/10/2021
En 2019, l’enquête publique avait donné des sueurs froides à Jean-Louis Verbrugge, patron de l’usine familiale créée par son grand-père il y a 80 ans, alors qu’il souhaitait déménager l’entreprise de Lille-sud à Templemars, dans un bâtiment déjà existant de la zone d’activités (un ex-entrepôt de Castorama). Le chef d’entreprise cherchait à quitter Lille-sud depuis pas mal d’années, les bâtiments historiques étant enclavés au milieu des logements, trop petits et peu accessibles.
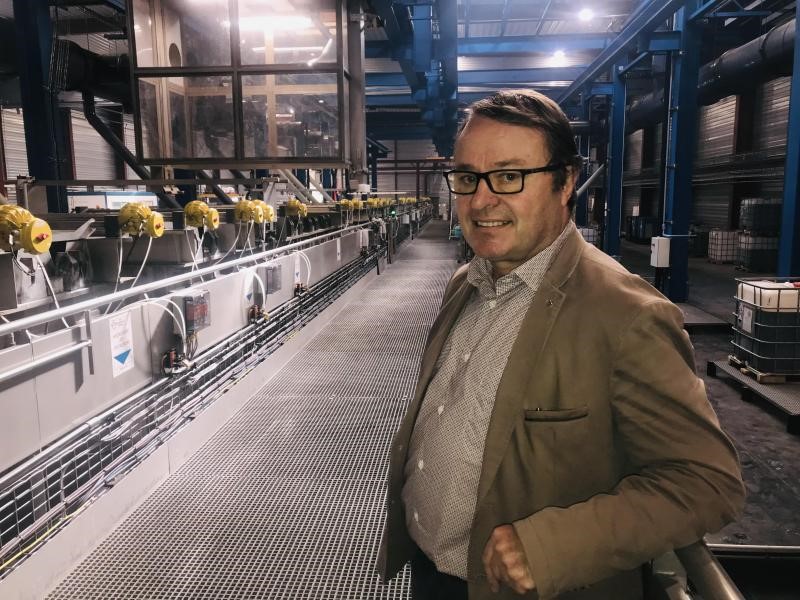
Un projet de mini forêt
L’usine chimique n’est pas classée Seveso (c’est le cas d’Air Product par exemple dans la même zone) mais soumise à autorisation préfectorale. Pas de risque d’explosion ici, mais des obligations de protection pour que les rejets d’eaux polluées n’aillent pas dans la nappe phréatique. On est ici au-dessus des champs captants (lire ci-contre). C’est ce qui avait fait tiquer l’opposition municipale de l’époque… devenue en 2020 majorité ! Depuis, les relations entre la municipalité et l’entreprise sont apaisées. Au point que le patron est allé aider lors de la plantation de la mini-forêt devant l’école et qu’il envisage d’en créer une sur l’espace vert de l’usine. Histoire de montrer qu’environnement et usine peuvent cohabiter.
Allonger la durée de vie des pièces industrielles
Que fait-on exactement chez Verbrugge ? L’usine applique des revêtements de nickel et de chrome sur des pièces destinées à l’industrie (auto, aviation, stations de forage, plasturgie, etc.). « On les protège de l’usure et de la corrosion, explique Jean-Louis Verbrugge, ingénieur Arts et métiers de formation. En clair, partout où ça coince, ça grince, ça couine ! Sans ce revêtement, en quelques semaines, les pièces d’acier s’useraient. » Tout se passe par électrolyse. La ligne de production se compose de dizaine de cuves, tandis qu’un robot vient tremper les pièces dans les différents bains. Ici, le chrome et le nickel (des minerais qui existent à l’état naturel) sont utilisés sous forme liquide.
« Il y a de la recherche pour remplacer le chrome VI, qui sera interdit en 2024. En attendant, on mise sur le nickel »
Tout est automatisé: un robot transporte les pièces d’une cuve à l’autre pour assurer le revêtement en nickel grâce à l’électrolyse.
Jean-Louis Verbrugge a limité le chromage et surtout développé le nickelage… Bien lui en a pris, car le chrome hexavalent utilisé dans ce type d’activité va être interdit en Europe d’ici 2024, « à cause d’un produit toxique à l’état liquide. Il y a de la recherche pour le remplacer. Pour l’instant, il y a des dérogations, par exemple, pour l’aviation, on n’a rien trouvé d’autre pour protéger les gros vérins du train d’atterrissage… »
Leader européen ?
Avec 40 salariés, Verbrugge semble une petite entreprise… mais importante sur ce marché de niche. « En France, on est quatre ou cinq. Avec nos nouvelles installations, on peut être les premiers en France voire en Europe. On a encore de la place et on peut répondre à des commandes en nombre. »
EN BREF :
L’histoire : Gaston Verbrugge a créé l’usine en 1941, reprise par son fils Jacques Verbrugge. Jean-Louis Verbrugge ne pensait pas reprendre les rênes… « Je suis venu pour aider à un projet. Et une fois que j’ai mis le doigt dans l’engrenage, je me suis pris au jeu, je ne regrette pas ! » L’homme de 57 ans est PDG depuis 1997.
Les salariés : ils sont 40 (20 en 1997), dont une dizaine d’encadrants et administratifs, et une majorité de personnes en 3-8 à la production, un ingénieur, des techniciens supérieurs et des techniciens non qualifiés, qui sont formés en interne, souvent après un bac pro.
L’investissement : il se monte à 6 millions pour la nouvelle usine de Templemars. La ligne de production a été doublée de 29 à 58 mètres.
Le chiffre d’affaires : 4 millions. En comparaison, en 1997, il était d’un million…
Les clients : pour le nickel, 30 % de l’activité concerne les pièces automobiles, 20 % pour l’industrie électronique (les machines qui fabriquent les processeurs par exemple) ; 15 % pour l’activité pétrolière (stations de forage) ; mais aussi dans le secteur médical, hydraulique, plasturgie, partout où les pièces sont soumises à la corrosion. Verbrugge n’a plus qu’une cuve pour le chromage en attendant son arrêt.
Quelles précautions pour les champs captants ?
« C’est impossible de polluer ! », s’engage Jean-Louis Verbrugge. L’usine chimique fait partie des installations classées pour la protection de l’environnement (ICPE) soumises à autorisation préfectorale. Le risque de cette activité chimique est la pollution de l’eau souterraine par les bains liquides. Or, trois barrières font dire au patron qu’il n’y a aucun risque. Première barrière : des « piscines » qui entourent chaque cuve. Deuxième barrière : le bâtiment lui-même est étanchéifié grâce à des seuils ou des barrières automatiques à chaque accès. Enfin, troisième barrière, si par exemple les pompiers étaient amenés à arroser les installations, l’eau qui déborderait du seuil irait directement dans un bassin de rétention. Celui-ci ne peut pas se déverser vers la nappe sans une action manuelle.
Par ailleurs, l’usine est équipée d’une salle de traitement des eaux polluées. Un système d’évaporation permet de séparer l’eau « pure » (qui est réutilisée) des matériaux polluants, qui sont recyclés par une entreprise spécialisée.
Articles en relations
Une pompe à carburant haute pression est indispensable au fonctionnement des moteurs modernes. Elle permet d’assurer débit et pression du carburant nécessaire à l’injection directe. La pompe, entraînée en rotation par l’arbre à cames, permet d’obtenir une pression d’utilisation dans la rampe d’injection de 120 bars.
Le 1er décembre est une journée tradition chez VERBRUGGE, nous célébrons Saint Éloi, patron des métallurgistes.