What is electroless Nickel plating ?
THE ONLY CORROSION PROTECTION COATING THAT IS ALSO WEAR-RESISTANT !
Electroless nickel plating is a metallic coating that protects any machine parts from corrosion and wear.
Superior quality corrosion protection
Electroless nickel plating is a metallic coating that protects any machine parts from corrosion and wear. In fact, it’s the only corrosion protection coating that offers very high hardness levels.
It can therefore be used to protect any metal mechanical components (steel, stainless steel, cast iron, aluminium or copper alloys) which, in addition to being exposed to oxidation, are subject to stress, strain, friction or even impacts.
Its other huge advantage lies in its application which doesn’t require electrolysis. It is applied by the contact of the product to be coated with the solution in which it is immersed.
As a result, the whole part, even if it has a complex shape (unless masking is required), will be coated very evenly without any edge or drip effects, providing full protection even in the smallest interior and exterior recesses.
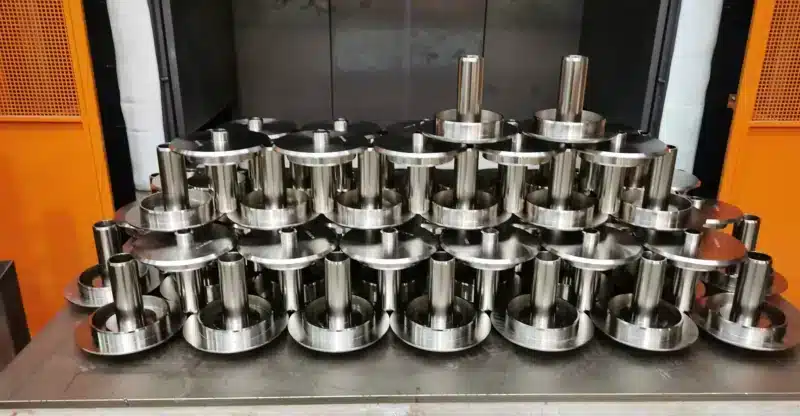
The different types of electroless nickel plating
There are three main families of electroless nickel plating that are differentiated by the nickel deposit phosphorus content:
– High phosphorus : the “Rolls-Royce” in terms of corrosion protection… which can also be hardened, or even more!
– Medium phosphorus: a compromise between hardness and corrosion protection. But is compromise a choice?
– Low phosphorus: very hard when it comes out of the bath, it is less resistant to corrosion.
These three families will soon be joined by the highly promising “composite nickels” (with particle additives) which are currently being developed by Verbrugge.
There are three main families of electroless nickel plating that are differentiated by the nickel deposit phosphorus content:
– High phosphorus : the “Rolls-Royce” in terms of corrosion protection… which can also be hardened, or even more!
– Medium phosphorus: a compromise between hardness and corrosion protection. But is compromise a choice?
– Low phosphorus: very hard when it comes out of the bath, it is less resistant to corrosion.
These three families will soon be joined by the highly promising “composite nickels” (with particle additives) which are currently being developed by Verbrugge.
Customised corrosion protection
Heat treatment after nickel plating can be used to further optimise the mechanical properties of the coatings depending on the part requirements.
We therefore have the option of privileging the coating hardness (see “hardened electroless nickel plating“) or its corrosion protection (see “diffused electroless nickel plating“).
Further details are available in our “in detail” section.